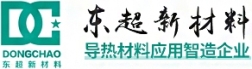
東莞東超新材料科技有限公司
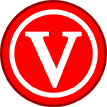
已認證
東莞東超新材料科技有限公司
已認證
氧化鋁導熱粉體因其廣泛來源和低成本,在聚合物基體中填充量較大,具有很高的性價比,因此成為制造導熱硅膠墊片最常用的導熱粉體。氧化鋁的形態(tài)有球形、角形、類球形等,不同的形態(tài)對熱界面材料的加工性能、應用性能、成本等有不同影響。此外,不同粒徑的影響也會在體系中形成一定的孔隙,影響導熱界面材料的導熱系數(shù)。本文將從以下幾個方面探討不同形態(tài)、不同粒徑的氧化鋁導熱粉體的搭配工藝,為制備高導熱硅膠墊片提供參考。
1. 在相同粒徑和添加量下,不同形態(tài)氧化鋁導熱粉體對導熱硅膠墊片加工性能的影響
選取5μm和45μm的球形、類球形和角形氧化鋁,在添加量為75%下測試其對導熱硅膠墊片加工粘度的影響。結果顯示,相同粒徑下,球形氧化鋁的加工粘度最小,而角形氧化鋁的加工粘度最大;相同形態(tài)下,粒徑越大,加工粘度越低。這主要是因為球形氧化鋁表面能較小,球的表面流動性更好,與基體攪拌成膜更均勻,因此體系粘度更低。而角形氧化鋁形態(tài)不規(guī)則,其顆粒表面能大,顆粒之間更易粘附,導致粘度更大。在相同形態(tài)下,粒徑越大,吸油值越小。
2. 在相同粒徑和不同形態(tài)下,不同添加量氧化鋁導熱粉體對導熱硅膠墊片導熱性能的影響
選取45μm的類球形、球形和角形氧化鋁,分別在75%、80%、85%的添加量下測試對導熱硅膠墊片導熱系數(shù)的影響。結果顯示,在相同添加量下,75%添加量時,角形氧化鋁制備的導熱硅膠墊片導熱系數(shù)較高。而在80%和85%的添加量下,類球形氧化鋁制備的導熱硅膠墊片導熱系數(shù)較高。隨著添加量的增加,三種形態(tài)氧化鋁制備的墊片導熱系數(shù)不斷升高。由于角形氧化鋁比表面積大,形成的導熱網絡更多,因此導熱效果較好。而類球形氧化鋁由于單晶顆粒、轉化率高、顆粒表面光滑,導熱系數(shù)最高。盡管球形氧化鋁球形度好,但轉化率較低且顆粒表面粗糙,導致導熱系數(shù)較低。
3. 在相同形態(tài)和不同添加量下,氧化鋁導熱粉體在不同復配比例下對導熱硅膠墊片導熱性能的影響
考慮最佳性價比和粉體顆粒堆積原理,選取45μm球形氧化鋁、45μm類球形氧化鋁和5μm角形氧化鋁以2:2:1、2:1:1、1:2:1、1:1:1的比例復配,分別在80%、85%、90%的添加量下測試對導熱硅膠墊片導熱系數(shù)的影響。結果顯示,在相同復配比例下,隨著添加量的增加,四種復配粉體填充的墊片導熱系數(shù)不斷增加。這是由于隨著粉體添加量的增加,顆粒之間的接觸點越多,逐漸形成致密的導熱網絡,因此導熱系數(shù)增加。另外,由于類球形氧化鋁的轉化率高,導熱系數(shù)高,因此其比例較大,導熱硅膠墊片導熱系數(shù)的提升越明顯。
4. 在相同添加量和不同復配比例下,復配氧化鋁導熱粉體堆積性能的影響
選取45μm球形氧化鋁、45μm類球形氧化鋁和5μm角形氧化鋁以2:2:1、2:1:1、1:2:1、1:1:1的比例復配。結果顯示,當球形氧化鋁、類球形氧化鋁與角形氧化鋁的比例為1:2:1時,堆積密度最大。這是因為顆粒之間的縫隙被相互填充,空隙小,密度大。
氧化鋁導熱粉體因其良好的導熱性能、電絕緣性、高硬度、強耐熱性和優(yōu)良耐磨性等優(yōu)點,被廣泛用作硅橡膠、橡膠、塑料、陶瓷、耐火材料等的填料。然而,為了得到廣泛應用,氧化鋁導熱粉體需要進行表面改性。
氧化鋁導熱粉體為什么要改性?
氧化鋁導熱粉體表面極性高,與高分子材料相容性差,在樹脂基體中很難分散均勻,加工難度增大,無法實現(xiàn)大量填充。此外,氧化鋁顆粒與樹脂表面張力差異導致高分子基體很難潤濕顆粒表面,使得二者界面處存在空氣間隙,界面熱阻增加,使得復合材料的力學性能和導熱性能等無法達到預期目標。
因此,必須對氧化鋁導熱粉體進行表面處理,降低顆粒之間團聚作用,改善導熱粉體與樹脂基體之間的相容性,提高粉體在樹脂基體中的分散性和
制作高導熱效率的導熱硅膠墊片,關鍵在于選擇合適的導熱粉末原料、確定粉體的形態(tài)和粒徑分布,這是一個多步驟的過程。東超新材在氧化鋁和氫氧化鋁等領域擁有超過十年的應用研究經驗,能夠根據(jù)客戶的具體產品規(guī)格、制造工藝和應用需求,提供定制化的導熱和阻燃高分子材料解決方案。
版權與免責聲明:版權歸原作者所有,轉載僅供學習交流,如有不適請聯(lián)系我們,謝謝。
最新動態(tài)
更多
虛擬號將在 秒后失效
使用微信掃碼撥號