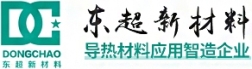
東莞東超新材料科技有限公司
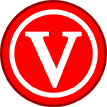
已認(rèn)證
東莞東超新材料科技有限公司
已認(rèn)證
一、不同形態(tài)的氧化鋁導(dǎo)熱粉對導(dǎo)熱灌封膠的影響
在導(dǎo)熱灌封膠的應(yīng)用中,不規(guī)則和球形氧化鋁導(dǎo)熱粉扮演著關(guān)鍵角色,但它們各自的優(yōu)勢和局限性也不同。不規(guī)則氧化鋁導(dǎo)熱粉以低成本和良好的熱穩(wěn)定性見長,但其導(dǎo)熱效率、分散性和流動(dòng)性較差,可能導(dǎo)致加工難度增加。相反,球形氧化鋁導(dǎo)熱粉在導(dǎo)熱性能、分散性、流動(dòng)性和力學(xué)性能方面表現(xiàn)優(yōu)異,但成本較高且在極端高溫下的熱穩(wěn)定性可能不如不規(guī)則形態(tài)??傮w來說,球形氧化鋁在提升灌封膠的綜合性能方面更具優(yōu)勢,而不規(guī)則氧化鋁則在成本敏感和高溫環(huán)境下的應(yīng)用中更為合適。
二、不同粒徑的氧化鋁導(dǎo)熱粉對導(dǎo)熱灌封膠的影響
不同粒徑的氧化鋁導(dǎo)熱粉對導(dǎo)熱灌封膠的綜合性能有著深遠(yuǎn)的影響,涵蓋了導(dǎo)熱效率、流動(dòng)性、加工難度以及產(chǎn)品的可靠性等方面。粒徑較小的氧化鋁顆粒因比表面積大,理論上能更有效傳導(dǎo)熱量,但過小顆??赡芤蚨逊e造成熱阻,反而降低導(dǎo)熱性;而大粒徑顆粒雖導(dǎo)熱性略遜,卻能形成更直接的導(dǎo)熱路徑。填充密度和流動(dòng)性方面,小粒徑粉末能提高填充密度但增黏降流,大粒徑則相反。加工性方面,小粒徑增黏不利于混合和澆注,大粒徑則改善加工性。力學(xué)性能上,小粒徑可能增強(qiáng)硬度和強(qiáng)度,而大粒徑可能提升韌性。熱穩(wěn)定性也受粒徑影響,小粒徑可能因反應(yīng)多而影響穩(wěn)定性,大粒徑則可能更穩(wěn)定。因此,要制備高性能導(dǎo)熱灌封膠,必須綜合考慮這些因素,并通過實(shí)驗(yàn)和理論研究確定最佳粒徑分布。
三、不同粒徑的氧化鋁復(fù)配對導(dǎo)熱灌封膠性能的影響
復(fù)合不同粒徑的氧化鋁對導(dǎo)熱灌封膠的性能影響頗為復(fù)雜,涉及填料填充效果、導(dǎo)熱路徑的優(yōu)化以及膠料整體表現(xiàn)。小粒徑氧化鋁能填補(bǔ)大粒徑間的空隙,增加填充密度,構(gòu)建出更緊密的導(dǎo)熱網(wǎng)絡(luò),從而提升導(dǎo)熱性。這種粒徑組合有助于優(yōu)化導(dǎo)熱系數(shù),小粒徑增強(qiáng)導(dǎo)熱性,大粒徑作為導(dǎo)熱節(jié)點(diǎn),合理配比能顯著提高導(dǎo)熱系數(shù)而不大幅增加成本。同時(shí),不同粒徑的復(fù)配還能平衡灌封膠的力學(xué)性能,小粒徑提升強(qiáng)度和硬度,大粒徑增加韌性。粒徑分布對流變性能也有影響,小粒徑增黏,大粒徑降黏,適當(dāng)復(fù)配可適應(yīng)加工需求。此外,合理的粒徑分布還能改善加工性能,減少混合和澆注阻力,提高效率。在成本方面,復(fù)配使用可以平衡性能與成本,大粒徑成本低,小粒徑成本高,通過配比實(shí)現(xiàn)經(jīng)濟(jì)效益。因此,通過實(shí)驗(yàn)和理論分析確定最佳粒徑分布和復(fù)配比例,是確保灌封膠性能最佳的關(guān)鍵。
為充分發(fā)揮不同粒徑氧化鋁導(dǎo)熱粉的優(yōu)勢,復(fù)配后的氧化鋁導(dǎo)熱粉在灌封膠中起到了以下作用:
提高灌封膠的導(dǎo)熱性能:不同粒徑的氧化鋁導(dǎo)熱粉相互補(bǔ)充,形成更加完善的導(dǎo)熱網(wǎng)絡(luò)。
優(yōu)化灌封膠的流動(dòng)性:復(fù)配后的氧化鋁導(dǎo)熱粉在一定程度上改善了灌封膠的流動(dòng)性,便于施工。
提高灌封膠的力學(xué)性能:不同粒徑的氧化鋁導(dǎo)熱粉復(fù)配,使灌封膠的力學(xué)性能得到提升。
四、不同添加量的氧化鋁對導(dǎo)熱灌封膠性能的影響
增加氧化鋁的用量能夠顯著提升灌封膠的導(dǎo)熱能力,然而,過量使用會(huì)導(dǎo)致灌封膠的觸變性能惡化,黏度上升,以及機(jī)械性能的下降。通過按質(zhì)量比2:1混合40微米和10微米的球形氧化鋁,研究了不同比例復(fù)配氧化鋁對灌封膠性能的影響,隨著復(fù)配氧化鋁用量的提升,膠料的導(dǎo)熱系數(shù)逐漸上升,抗沉降性改善,但同時(shí)膠料黏度也在增加。
氧化鋁導(dǎo)熱粉的添加量對灌封膠的導(dǎo)熱性能和力學(xué)性能具有重要影響。
添加量較少:導(dǎo)熱性能較差,但灌封膠的力學(xué)性能較好。
添加量適中:導(dǎo)熱性能較好,灌封膠的力學(xué)性能適中。
添加量較多:導(dǎo)熱性能最佳,但灌封膠的力學(xué)性能較差。
這一現(xiàn)象的原因在于,膠料中的熱量傳遞主要依賴于聲子傳遞,當(dāng)氧化鋁用量較少時(shí),填料能夠在膠料中均勻分散,填料粒子之間缺乏接觸和相互作用,導(dǎo)致導(dǎo)熱系數(shù)較低。隨著導(dǎo)熱填料用量的增加,填料粒子開始相互接觸,形成鏈狀或網(wǎng)狀的導(dǎo)熱路徑,從而顯著提高了膠料的導(dǎo)熱率。然而,當(dāng)填料用量超過一定閾值后,膠料的黏度增加,觸變性能變差,使用過程中容易產(chǎn)生氣泡,或者由于涂抹不均而影響散熱效果。這些問題都是高導(dǎo)熱填料需要解決的問題,例如使用我們東超高導(dǎo)熱灌封膠粉體填料,是針對粘度上升問題通過特殊技術(shù)粉體填料表面處理,明顯改善了黏度問題。
五、用不同的硅烷偶聯(lián)劑處理填料對膠料性能的影響
硅烷偶聯(lián)劑在灌封膠中起到改善填料與基體界面結(jié)合的作用,從而提高灌封膠的性能。無機(jī)填料在有機(jī)硅聚合物體系中的分散性通常不佳,為了改善這一問題,需要采用硅烷偶聯(lián)劑對無機(jī)填料進(jìn)行表面改性處理。這一處理過程旨在填料表面引入非極性基團(tuán),增強(qiáng)其親油性,從而在硅氧烷體系中獲得良好的浸潤性,實(shí)現(xiàn)均勻分散。這樣做不僅增加了導(dǎo)熱填料的用量,還提升了導(dǎo)熱系數(shù)。表面改性處理劑的選擇對導(dǎo)熱灌封膠的性能有著直接的影響。相較于未處理的填料,經(jīng)過處理的填料與有機(jī)硅氧烷之間的界面張力減少,分散性顯著提高,粒子間的黏結(jié)聚集現(xiàn)象減少,膠料的黏度也隨之降低。
采用不同硅烷偶聯(lián)劑對填料進(jìn)行處理,對膠料性能產(chǎn)生顯著影響。硅烷偶聯(lián)劑通過在無機(jī)填料表面形成有機(jī)層,增強(qiáng)其與有機(jī)聚合物基體的界面兼容性,不同偶聯(lián)劑的化學(xué)結(jié)構(gòu)和官能團(tuán)決定了它們與基體的相互作用力。此外,偶聯(lián)劑降低了填料表面的極性,提升了在有機(jī)溶劑和聚合物中的分散性,尤其是長鏈烷基硅烷偶聯(lián)劑,能有效降低膠料黏度,提升加工性能。處理后的填料能更有效地傳遞應(yīng)力,增強(qiáng)膠料的機(jī)械性能,而不同偶聯(lián)劑對膠料的彈性模量、抗拉強(qiáng)度和沖擊強(qiáng)度影響各異。硅烷偶聯(lián)劑還能改善填料的導(dǎo)熱網(wǎng)絡(luò),影響導(dǎo)熱系數(shù),并提高膠料的耐熱性和耐化學(xué)性,這取決于偶聯(lián)劑的化學(xué)結(jié)構(gòu)和反應(yīng)性。最后,偶聯(lián)劑的加入會(huì)影響膠料的流變性能,如降低黏度和改善觸變性,不同偶聯(lián)劑對工藝性能的影響需根據(jù)應(yīng)用需求來選擇。因此,挑選合適的硅烷偶聯(lián)劑進(jìn)行填料處理,是提升膠料性能的關(guān)鍵。
最新動(dòng)態(tài)
更多
虛擬號將在 秒后失效
使用微信掃碼撥號